Vacuum Forming
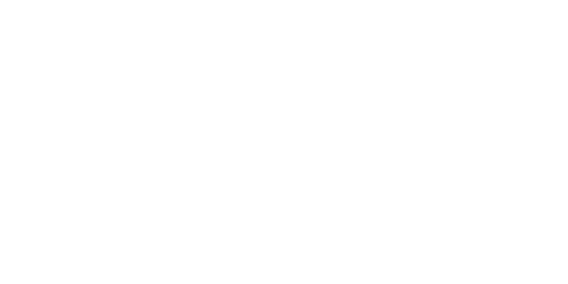
Here at Tasman, we are especially proud of our partners in the vacuum and thermoforming industry, Formech & GN.
Formech vacuum formers are used the world over! Applications in technical and deep draw vacuum forming are where Formech excels. From desktop, student friendly formers through to large sheet industrial vacuum formers for commercial and engineering applications, Formech have a model to suit virtually every need. With hundreds of Formech vacuum formers in operation across Australia and New Zealand, Formech is a name you can trust.
GN Thermoforming is known worldwide for high-speed thermoforming for food packaging applications. From berry and fruit trays, clam shell applications for a variety of food packaging, GN offer Form-Cut-stack and cut in place and contact heat machines & tooling.
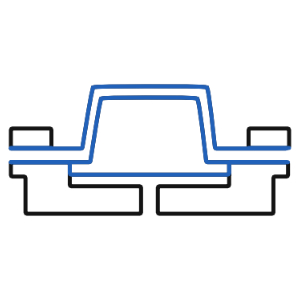
A step-by-step description of the vacuum forming process:
-
Mould Preparation: The process begins with the preparation of a mould, which can be made of various materials such as wood, epoxy, or aluminum. The mould is typically created to match the desired shape and size of the final product.
-
Thermoplastic Sheet: A flat thermoplastic sheet, often made of materials like ABS, polystyrene, or acrylic, is clamped or secured in a frame above the mould. The sheet should be larger than the mould to ensure adequate coverage.
-
Heating: The thermoplastic sheet is heated until it reaches a pliable state. This can be done using various methods, such as infrared heaters or radiant heating elements. The sheet needs to be heated evenly to avoid any inconsistent forming.
-
Forming: Once the sheet is heated and softened, it is lowered or moved down towards the mould. At this stage, a vacuum is applied between the mould and the sheet, drawing the heated material tightly against the mould’s contours. The vacuum helps shape the plastic to match the mould’s surface and creates a detailed replication of the mould’s shape.
-
Cooling: After the forming process, the vacuum is released, and cool air or water is used to rapidly cool the plastic, solidifying it into the desired shape. Cooling time varies depending on the thickness and type of thermoplastic material used.
-
Trimming: Once the plastic has cooled and solidified, excess material or flash around the edges is trimmed off to achieve the final shape of the product. This can be done manually or through automated trimming equipment.
-
Finishing: Additional finishing operations, such as drilling holes, adding logos, or applying surface finishes, may be performed depending on the requirements of the final product.
Get Started